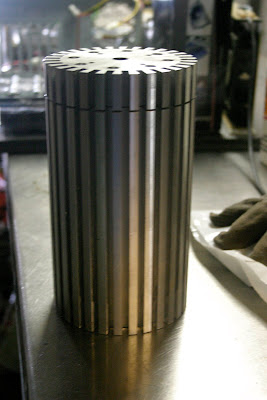
Then to the case building. First I took measures of the preliminary layout I had on the table and cut the L-beams to size. After cutting I polished the rust off the ends so that they would be easier to weld and the weld quality would be better too.
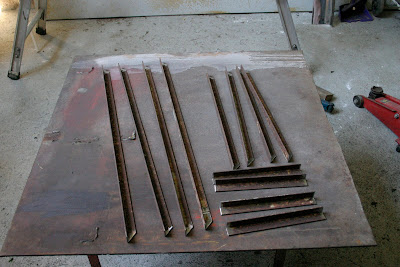
Then I had to ask my dad to be the extra pair of hands for me. I might have been able to do the case frame by myself, but having someone holding the pieces together instead of clamping them on that makeshift table of mine sounded a way better idea.
First we put just a little drops on every corner so we were able to adjust the frame pieces before welding them together. This part was painstaking, because all the corners had to be totally right or the frame would become warped and the covering plates would then look very ugly. After a lots of measuring and bending with comments like "Are you sure about that?", "That's not going to work" and "Seems like you've learnt something", we were ready to finish the frame parts. Luckily I had cut all the pices at the same length within 1mm. If there'd been bigger difference the process of putting the frame together would've been impossible and I'd still had to cut them to same length at some point.
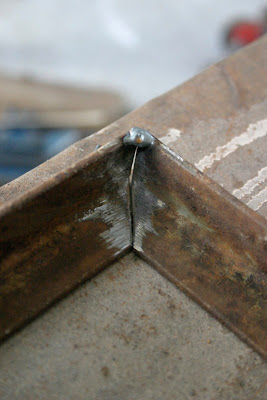
We welded the opposite corners together so the warping would be minimal.

First part ready.
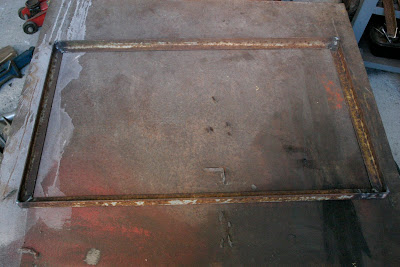
We also welded the other side to make the joint stronger.
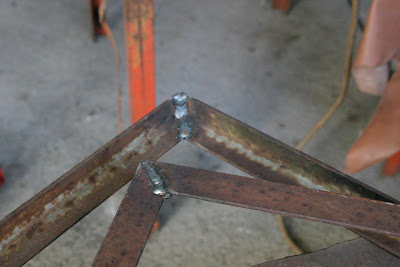
Both ends ready. The next thing was to put them together and that proved to be a bit more difficult than I had thought. More about that in the next entry.
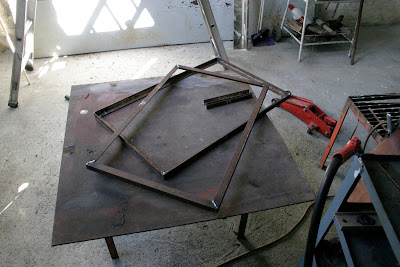
No comments:
Post a Comment